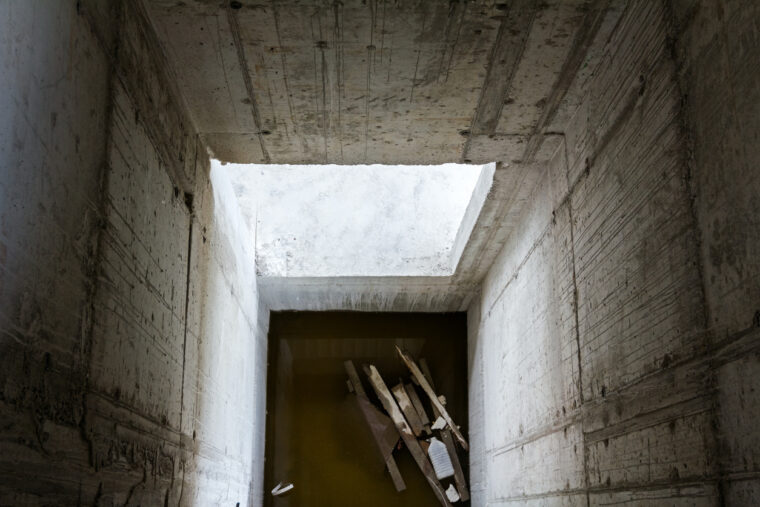
High-rise buildings, and the many companies that occupy them, have become a hallmark of the modern world. While these structures are awe-inspiring, they also come with their own unique challenges — one being elevator maintenance.
Elevators are a critical part of any high-rise building, and ensuring they are always in working order is essential for the safety and productivity of the people who work in those buildings. A malfunction may be mechanical, but water intrusion or flooding of the elevator pit could cause the elevator system to shut down until the problem is resolved.
What is an Elevator Pit?
The elevator pit is the space between the shaft’s lowest landing door and the ground at the bottom of the shaft. It consists of a concrete base slab, as well as four concrete or concrete block walls. A sump may be required in some situations, and if the pit is built for a hydraulic piston elevator, there will also be a center casing for the piston shaft elevator.
Elevator pits serve several important functions. They help support the elevator shaft, and they also help keep water and debris from entering the elevator shaft. In addition, elevator pits help provide a buffer between the bottom of the elevator car and the floor of the building. This can help prevent damage to the elevator car or the building if the elevator car should happen to fall.
Elevator pits must be carefully constructed to perform these functions effectively. The walls of the pit must be strong enough to support the weight of the elevator shaft and car, and they must be sloped so that water does not pool inside the pit. In addition, elevator pits must be waterproofed to prevent water from entering the elevator shaft and damaging the equipment inside.
The Importance of Waterproofing Elevator Pits
Concrete is created when cement, sand and gravel are combined with water. When the water evaporates or dries, it leaves gaps between the particles that are filled with air. Despite not seeing a water leak right away through a slab of concrete, water does get through the spaces between the particles.
Water can gradually dissolve the concrete over time, causing it to fracture and allowing the water to seep through the wall or floor. This makes concrete permeable, rather than waterproof. Therefore, precautions must be taken to keep the water out of the elevator pit.
You can either waterproof your elevator pits from the outside (positive-side waterproofing), which is the best approach to keep concrete, steel and interior areas safe or you can do it from the inside (negative-side waterproofing). By using proper application procedures with positive-side waterproofing, you’ll achieve maximum performance from your system.
4 Elevator Pit Waterproof Tips
1. Annual/Frequent Inspections
Each state has its own laws and regulations regarding elevators, but some states allow significant gaps between inspections. The longer between inspections, the more likely you are to develop a water problem. Instead of waiting for mandated checks, check your elevator pits after it rains for a day or two to ensure there isn’t any water there. If your elevator pits don’t get frequent leaks or signs of neglect, it will be easier to remove the water from them.
2. Apply a Membrane
Applying a membrane waterproofing material to the exterior surface of an elevator pit foundation is an excellent way to prevent water infiltration. Most membranes are applied when a building is constructed, but some older buildings might require one to keep water out of the foundation.
3. Above and Below Grade Foundation Waterproofing
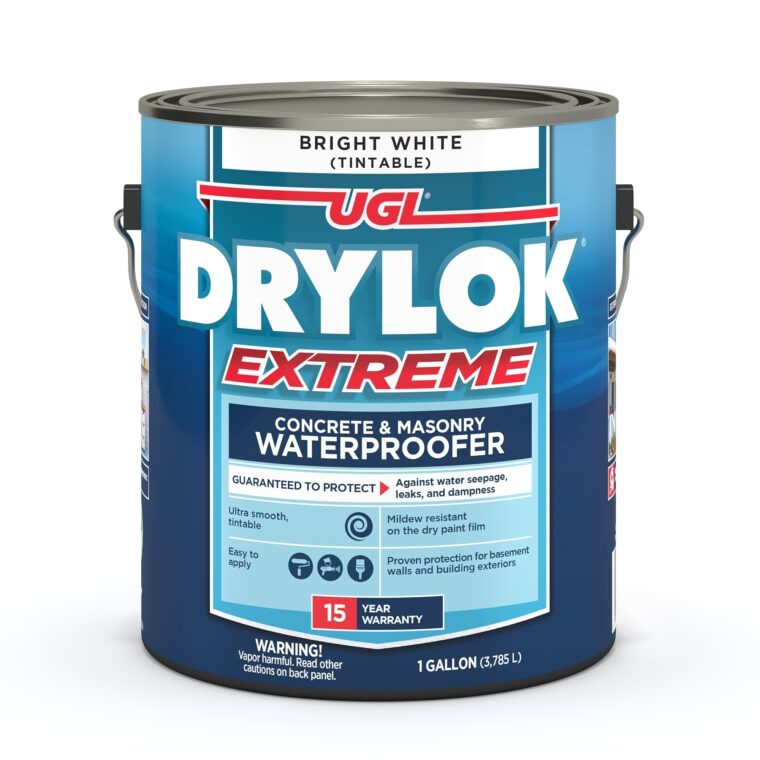
Above-grade foundation waterproofing is a method of protecting elevator pits from water infiltration from surface water sources, such as rain runoff. There are many products on the market that can be used for this purpose, including DRYLOK®. These products are applied as a coating to the exterior and interior of elevator pit walls and floor and work to prevent water from penetrating the concrete.
Below-grade foundation options include waterproofing coatings like DRYLOK Extreme, as well as membrane waterproofing materials like Bentonite and drain tile systems.
4. Utilize Drain Tile Systems
These systems can be installed along the walls of an elevator shaft to help control water intrusion into elevator pits. The steps to install them include:
Cutting out a trench in the concrete along the interior or exterior walls.
Draining any water present along the concrete foundation.
Adding a waterproof membrane against the interior of the foundation to create a waterproof barrier
To finish, a perforated drain tile is placed in pea rock and wrapped with geo fabric to create a water filter that flows well. This leads to a sump pump, which then sends the water outside the building or into the storm sewer.
Even though they aren’t always ideal because of how much work goes into installing them and they don’t seal the concrete foundation completely, drain tile systems are great elevator pit water solutions for when everything else fails.
Achieve Superior Waterproofing of Elevator Pits with DRYLOK
Looking for a waterproofing solution for your elevator pit? Look no further than DRYLOK! We have the ideal waterproofing solutions to help safeguard your elevator. Our flexible encapsulated polymers provide a smooth, waterproof finish that is perfect for any surface, including cinder and concrete block, stucco, brick and bare concrete.
Whether you are looking to protect your interior or exterior surfaces or above- or below-grade masonry, we have you covered. Contact us today for more information and where to find our products near you.