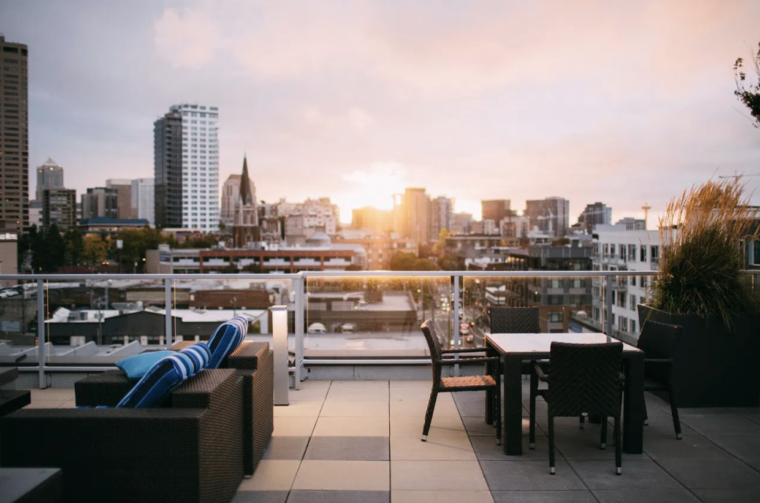
Rooftop decks, constructed from masonry, are becoming an increasingly popular architectural trend in urban residential and commercial buildings.
As cities continue to evolve and space becomes a premium, decks provide valuable outdoor space without sacrificing building footprint. However, the exposure to weather elements makes these types of structures highly susceptible to water damage.
A proper waterproofing regimen is crucial for the longevity of the deck and the overall structure it is built upon. To achieve the best results, it’s essential to understand the process of waterproofing your rooftop deck and the different materials and techniques available.
Assessing Your Rooftop Deck
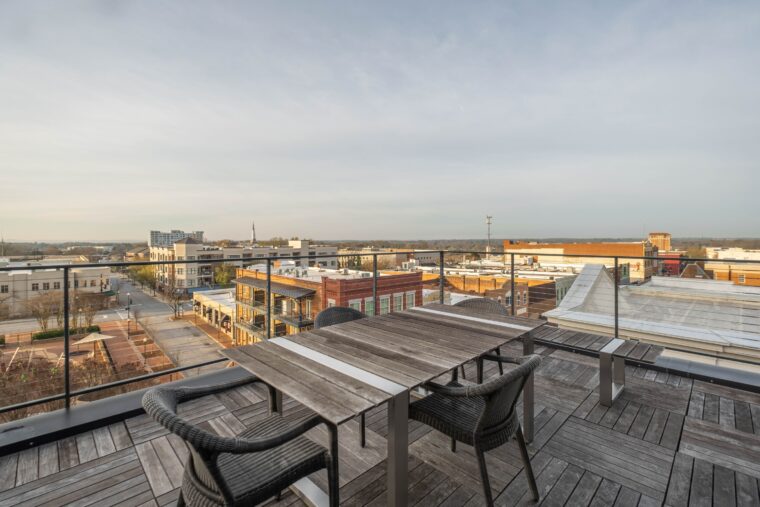
Inspection
Before starting a waterproofing project, it’s essential to inspect your rooftop deck thoroughly. Look for signs of water damage like discoloration, peeling paint or soft spots on the deck’s surface. Check for cracks or gaps in the sealant around flashing and joints, as they allow water to enter. If your deck has a slope, ensure it directs water away from the building and doesn’t create pools.
Dealing with Existing Wood Decking and Pavers
If your rooftop deck features masonry pavers or wood decking overlay, they must be removed before the waterproofing procedure. This is essential to ensure thorough sealing of the underlying substrate, which will provide a robust barrier against water ingress and subsequent damage.
Types of Waterproofing Systems
Liquid-Applied Membranes
Liquid-applied membranes are an effective waterproofing system for rooftop decks. They commonly consist of a primer coat and two top coats applied directly to the deck’s surface.
Sheet Membranes
Sheet membranes are another practical option for waterproofing rooftop decks. Typically made from rubber, plastic, or bituminous material, sheet membranes are rolled onto the deck surface and bonded to the substrate using an adhesive. The sheets overlap at the edges to create a continuous watertight barrier.
Sheet membranes are highly durable and resistant to UV light, making them an excellent choice for sun decks. However, their installation can be more complex than liquid-applied systems, especially around corners and details.
Liquid Applied Waterproofers
Liquid-applied waterproof coatings are a versatile and economical solution for waterproofing masonry rooftop decks. One very effective product is DRYLOK Floor and Wall, if you are laying pavers or wood decking on top or leaving as a finished coat. You can also use DRYLOK Siloxane 7 on bare, etched concrete decks if you want a protective, weatherproof, transparent finish. For a decorative finish, you can paint over the DRYLOK Floor and Wall with DRYLOK Concrete Floor Paint or lay wooden decking, pavers, etc., over the waterproof coating. Free-floating decking or pavers are best as not to damage the continuous waterproof coating.
Latex-based product with an easy application process, typically requiring two coats applied with a brush, roller, or sprayer
A smooth, waterproof finish works well for exterior masonry surfaces, which makes it an ideal choice for rooftop decks
Fills hairline cracks
All DRYLOK coatings are resistant to UV light to help reduce the risk of color fading and damage from the sun.
Preparing the Rooftop for Waterproofing
Cleaning and Removing Debris
Cleaning and removing debris from your rooftop deck is a critical step in the waterproofing process. Start by sweeping the surface thoroughly to remove loose dirt, leaves, and other debris. If there is embedded dirt or stains, use a wire brush and a suitable etching solution.
Addressing Structural Issues or Damage
Before proceeding to the waterproofing step, any structural issues or damages to the rooftop deck must be addressed.
New Rooftop Sun Deck
If installing a new rooftop deck, ensure the existing roof structure can handle the extra weight. You may need to have an engineer evaluate the structure and provide documents showing that it is sufficient for the new project.
Existing Rooftop Sun Deck
For masonry pavers, keep an eye out for pavers that have become loose or have shifted out of place. After the waterproofing is complete, these corrections should be implemented. Make sure that any cracks or gaps are filled in.
Filling Cracks and Leveling the Surface
Before you start waterproofing, it’s crucial to clean up cracks and level the surface. Cracks and uneven areas can affect the effectiveness and durability of your waterproofing products. For a reliable solution, check out DRYLOK Pourable Masonry Crack Filler.
It is manufactured specifically to fill and seal minor cracks in concrete surfaces like sidewalks, patios, and garage floors. DRYLOK Crack Filler provides a smooth finish that can be painted over once it’s dry, and it’s designed to withstand the elements. For the best results, remember to clean the crack and remove any loose material before applying it.
Ensuring Proper Drainage
Adequate drainage prevents standing water, which could lead to leaks, premature wear and tear, and structural damage. Begin by examining the slope of the deck. Ideally, your deck should slightly tilt towards the drainage point to facilitate the natural flow of water.
If your deck is level or has low spots, consider consulting a professional to adjust the slope. To prevent blockages, regularly inspect and clean your deck’s drainage system, including gutters and downspouts.
Removing Existing Coatings or Finishes
Before applying new waterproofing, it is necessary to remove any existing coatings or finishes from the deck surface. These could potentially interfere with the adhesion and effectiveness of the new waterproofing products. Begin by using a paint scraper or a pressure washer to remove loose or flaking paint.
To strip stubborn coatings, consider using a chemical paint stripper designed explicitly for masonry surfaces. Once the old coating is entirely removed, clean the substrate for the waterproofing product. Rinse the deck thoroughly to remove any lingering dust or debris, and then allow the surface to dry completely.
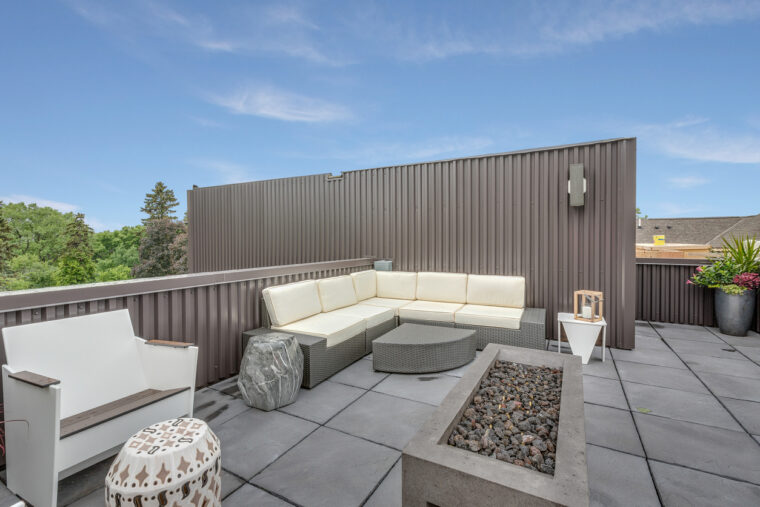
The following are general guidelines for applying waterproofing products:
For the best results, it’s recommended to schedule your project when the air and surface temperatures are 50°F or higher to help ensure the optimal outcome and desired quality.
Choose a rain-free period for application.
Thoroughly stir the product without thinning it before and during the application of DRYLOK Masonry Waterproofer or DRYLOK Siloxane 7.
For the first coat on bare masonry, use a three-quarter-inch nap roller, a DRYLOK Brush, or a quality nylon bristle brush. If using a brush, work the waterproofer into the masonry’s pores and make sure to fill all pores and pinholes. If using a roller, back brush the first coat for the same result.
Allow the first coat to dry for 2 to 3 hours before applying a second coat.
The second coat can be applied using a roller, brush or sprayer. Note that a minimum of two coats is required for warranty waterproofing. After the second coat, carefully inspect the entire surface for pinholes and apply an additional coat if needed.
*Be sure to follow the product label for the desired coating for more specific preparation and application steps
If leaking persists after two coats, it indicates that pores or pinholes are still open, and these areas should be repainted.
Post-Installation Considerations
Regular Inspections and Maintenance
The cornerstone of a healthy rooftop deck is regular inspections and proactive maintenance. Inspecting your deck for signs of wear or damage, such as cracking, peeling, or discoloration, should be done at least twice a year, ideally in spring and fall. During the inspection, check for loose railings, protruding nails, or rot and take prompt action to resolve any issues found.
Cleaning Schedule and Products
A clean deck not only looks good but also lasts longer. Plan to clean your deck thoroughly at least once a year. A mild, non-abrasive cleaner suitable for masonry, it is ideal for lifting dirt and mildew without damaging the surface. Make sure to rinse the deck thoroughly after cleaning to avoid any residue build-up, which can lead to staining.
Handling Minor Repairs
To prevent further damage, address minor repairs as soon as they arise. When using repair products, always follow the manufacturer’s instructions.
Reapplying Waterproofing
Depending on the weather exposure and deck usage, you may need to reapply a waterproofing treatment every 2 to 3 years. Ensure that the deck surface is clean and dry before reapplication. Follow the manufacturer’s instructions for the best results.
Protecting Rooftop Furniture and Features
Furniture and other features on your rooftop deck are exposed to weather and need protection. Consider covering furniture when not in use and applying suitable protective treatments to other features as necessary.
Trust in DRYLOK for the Best in Waterproofing for Your Rooftop Deck
When it comes to safeguarding your rooftop deck from the elements, DRYLOK is a reliable and long-lasting solution. Our waterproofing products are designed with durability and ease of use in mind to help ensure that your deck remains dry, safe, and in excellent condition, regardless of the weather.
Contact us today to locate a retail supplier near you!